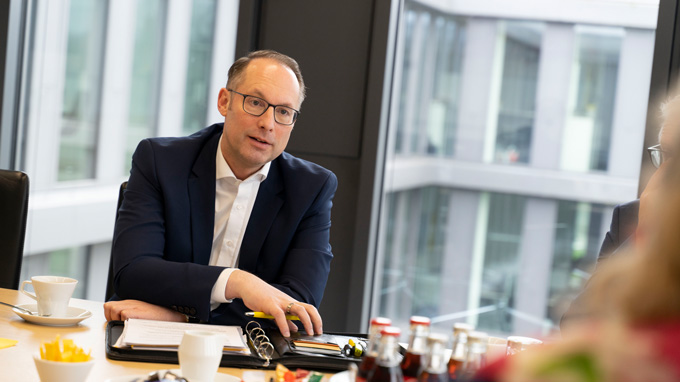

Christian Wolf sees Turck well prepared for the challenges of these times
Digitalization and Automation are the Bridges to Sustainability
Despite the risks and uncertainties of war, the energy crisis and disrupted supply chains, the automation industry can look back on two good years. Christian Wolf, Managing Director of Turck, and Bernd Wieseler, Product Manager for the RFID segment at Turck, discuss the boom in automation technology, the path to sustainability and the challenges that the digital transformation poses for large companies and SMEs in an interview with Anja Van Bocxlaer, Editor-in-Chief of the Think WIOT Group.
Mr. Wolf, what challenges did Turck have to overcome in the past three years of crisis?
Wolf: The past three years have definitely been challenging years in terms of the scarcity of resources, the shortage of skilled workers and the uncertain overall situation – caused by Corona and the war. Three years with ups and downs. As an example: in my 25 plus years at Turck and in the industry, I have never experienced such a price and procurement war for components as in 2021 and 2022. Brokers determined many prices for components and raw materials, which we had to process in close cooperation with our customers.
How has the crisis affected business development?
Wolf: In business terms, we have experienced exactly the opposite of a crisis in these years, namely a boom in automation technology. In 2020, sales fell slightly compared to the previous year. In 2021, we recorded growth of 26 percent in automation technology. In 2022, we still had a very good 16 percent in growth. A curious circumstance. The period of the pandemic is actually the most successful period in our company's history to date. The question of how we can counteract the shortage of employees, the shortage of materials and the lack of manufacturing capacity, especially during the pandemic, arose at the same time as the massive increase in incoming orders.
What do you see as the reasons for the increased demand for automation solutions?
Wolf: There are several reasons. Generally speaking, automation technology offers solutions to many of the problems we face today. Specifically, the four major social and economic challenges of this era are: de- globalization with intensive global trade interdependencies, decarbonization and thus the pursuit of CO2 neutrality and energy efficiency, and the transformation toward electromobility. The automation and digitization of all processes is the basic prerequisite for each of these tasks. And with all these changes, we must also successfully address demographic transformation.
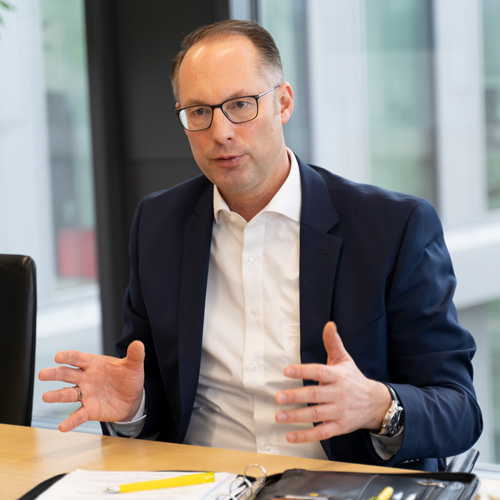
Can you give an example of how digitization and automation relate to the issue of sustainability?
Wolf: Let's take the example of mechanical engineering. Today, due to increased energy prices on the one hand and EU sustainability requirements on the other, a mechanical engineering company is asking itself how it can make production more energy efficient. The answer is: through digitization and automation. The evaluation of sensor data from machines is essential to set up process speeds as well as the maintenance and downtimes of machines in such a way that the energy balance is optimal. The use of energy can also be optimized through the use of automation technology. Reducing energy consumption and operating costs are processes that can ultimately only be solved in a data-based manner through digitization. In this respect, efforts to produce and manage sustainably are significant accelerators for digital transformation in industry.
How has the increase in energy prices affected production at Turck?
Wolf: Not as strongly as in other industries, but the increased costs are also noticeable for us. Turck is not a company with high energy consumption. We only use gas to a small extent, not for machines and plants, but to heat our premises. Our machines and plants are operated electrically. We have therefore launched initiatives and investments to significantly increase the share of photovoltaics in our energy supply in the near future. In doing so, we want to become much more self-sufficient in terms of energy. I generally welcome the fact that an ecological rethinking of energy issues is taking place in industry in order to become less dependent on gas supplies in the future.
Do you see a way to build resilience against the impact of geopolitical crises?
Wolf: If you assume that economic development will remain volatile, you have to position yourself more broadly on the capacity side in order to respond quickly to customer requirements in the event of a sharp rise in demand. After all, high availability will continue to be a decisive criterion for the economic success of companies in the future.
Ultimately, this means acting countercyclically. In other words, it will continue to be the case that the economic climate will cool down after three to four years. To nevertheless be able to plan for the longer term, we at Turck are now working on a structured five-year plan. As a company, we have to turn the uncertainties caused by geopolitical tensions back into entrepreneurship and stay on the investment path even in difficult times.
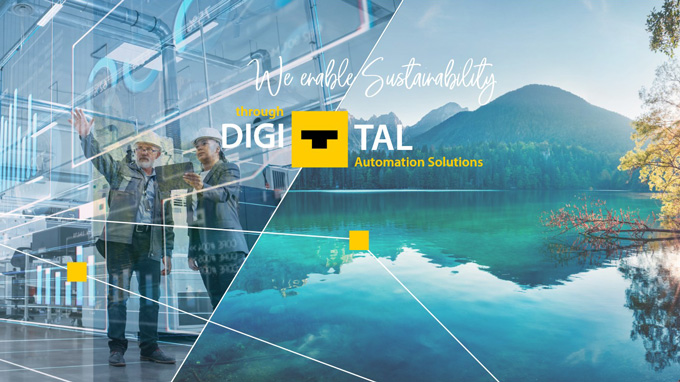
Mr. Wieseler, how did product development 2022 turn out at Turck?
Wieseler: Most of our development capacity has gone into the redesign of existing circuits and layouts in order to remain in a position to deliver despite missing or extremely overpriced components. In addition, we have developed many firmware updates to optimize the IIoT functionalities of our solutions. Take the RFID interfaces in IP67, for example: We have expanded them with OPC UA to include the AutoID Companion Specification V. 1.01 and an HF bus mode. This enables smooth and direct communication with MES, PLC, ERP or cloud systems.
Another example is the HF bus mode of our RFID interfaces, which offers great time and cost advantages for applications with many reading points. This allows up to 32 HF read/write devices per channel to be connected in series simply by means of a T-piece. Via OPC UA we connect the devices with simple methods and get easier access even for smaller applications.
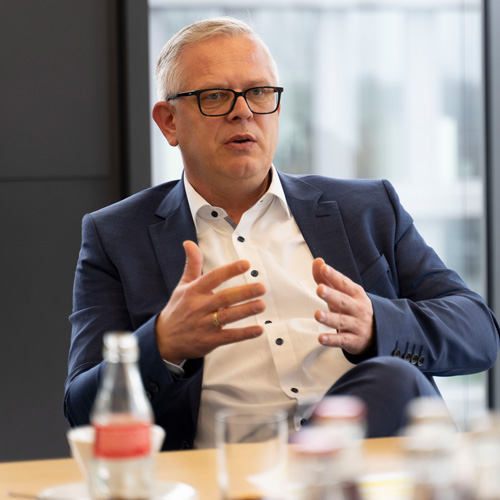
Will Turck offer software products more frequently in the future?
Wieseler: We use software to connect systems and to make it as easy as possible for the customer to use our products. However, we are first and foremost a hardware manufacturer and the software is always directly related to our hardware. With TAS, the Turck Automation Suite, for example, we help our customers make as much as possible out of their Turck devices. Although software development plays an extremely important role in our products, it does not mean that we are a system house.
Can you explain the TAS?
Wieseler: With pleasure. TAS is an IIoT platform that simplifies the management and configuration of Turck devices in industrial Ethernet networks. With TAS, the commissioning phase is simpler thanks to visualization, but also faster thanks to batch functions, such as firmware updates or the assignment of IP addresses. We thus generate added value for the customer because they can get an overview of all products with one platform and address them. We had already integrated many examples and usable applications in the first version, including a simple visual representation of proofs of concepts with our products. Being able to easily address RFID applications and devices is a very big topic in the development work of TAS.
Why was the focus on an improvement in the RFID segment necessary?
Wieseler: Setting up an RFID gate involved a lot of effort. The customer first had to align his antennas. Then find out which tag was captured and where it was located. Based on this, initial conclusions could be drawn. However, it was all presented in a relatively rudimentary way. In the new version, we are providing better tools in TAS that capture and display the processes on the individual levels in such a gate. How the data carriers are read in the levels can be represented two-dimensionally or three-dimensionally. This representation helps our customers.
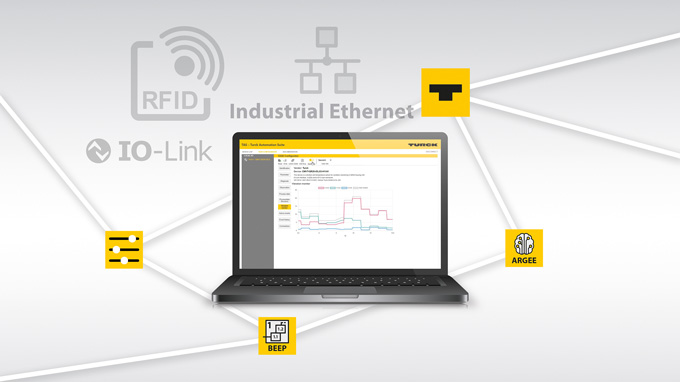
What does the customer learn by gaining insight into different levels?
Wieseler: Via the position of the tags. When I bring a pallet with several products through the gate, for example, the customer sees how many can be read from the front, in the middle or at the back. The customer sees what field strength is needed and then knows where the antenna position should be adjusted.
How does TAS support customers in reading data carriers as energy-efficiently as possible?
Wieseler: We also have a new tool for this. In the past, high performance and low power consumption were often mutually exclusive. The new tool uses a readout cycle, which we call 'power sweep', to determine which parameters result in the best read performance and how data carriers are optimally controlled.
How strong is the RFID segment at Turck at the moment?
Wolf: We are experiencing enormous growth and full order books. On average, we have grown by 25 percent or more in the RFID segment every year, and by almost 75 percent in the last two years. Turck has equipped many new plants with RFID, especially in intralogistics. However, we were unfortunately limited in our capacities and had to turn down orders as a result. In 2022 in particular, RFID products were severely affected by delivery problems and material shortages, especially for chips.
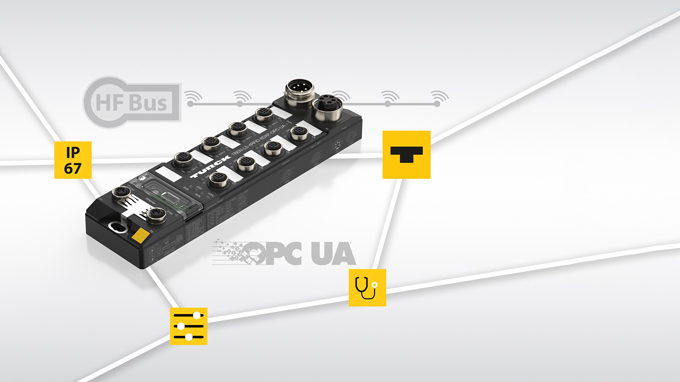
Full steam ahead with sustainability and digitalization – this sounds like a happy ending. Is it?
Wolf: Yes, there are indeed a great many opportunities arising from digitalization and sustainability, but this does not apply to every industry. Energy-intensive companies face major challenges, including economic ones. But transformation also means investing. For example, an automotive supplier that generates 90 percent of its sales today with a transmission line that will be eliminated in five or ten years as part of the e-mobility turnaround must demonstrate a transformation speed that is very difficult to manage.
So what does this mean for providers who are unable to invest sufficiently in this transformation?
Wolf: This is difficult for many SMEs. Large companies sometimes assign entire teams of employees to study all the regulations and develop implementation plans. At Turck, we still manage it – with effort and investment. However, as a smaller energy-intensive company with 50–100 employees, for example, becoming climate-neutral by 2030 and complying with all the EU regulations is a major challenge.
What does this mean for the EU and for Germany? After all, SMEs account for over 90 percent of companies in Germany.
Wolf: I believe that the topic of 'sustainability' can be a real competitive ad- vantage for the EU. However, there are requirements in EU legislation that are hardly feasible by 2030. With the supply chain law, for example, it will be very difficult to determine how high (or rather how low) the CO₂ emissions are along the entire supply chain down to the smallest detail for every component. There is not enough time for that.
Do you see a threat to Turck's position in this scenario?
Wolf: No. Let's take a concrete example like the digital nameplate. The nameplate contains information about the product and its entire life cycle. Companies of our size and with the diverse competencies available will realize this and will even generate competitive advantages from it. I believe that the requirements for a digital nameplate with a product carbon footprint that can be credibly proven are difficult for an SME to achieve. For this, all product data would have to be digitized and supply chains would have to be seamlessly checked.
What do you base your assessment on?
Wolf: I am active in Mülheim on a voluntary basis in the Zenit e.V. network. Zenit is the Center for Innovation and Technology in NRW, which offers companies a platform for networking, internationalization and the transfer of know-how and is particularly geared toward SMEs. Many of the small and medium-sized companies I come into contact with there are still partly unaware of what lies ahead for them.
They are faced with a mountain of regulations and in some cases have neither the know-how nor the human resources to implement them in a timely manner and therefore need external support. This is why policymakers are called upon to find more differentiated approaches for industrial companies.
Author | The interview was conducted by Anja Van Bocxlaer, Editor-in-Chief and owner of the Think WIOT Group
- Technologies
- Asset Monitoring Gateway with Cloud ID
- Asset Monitoring Gateway with SNAP ID
- Codesys
- Condition Monitoring
- Ethernet in Hazardous Locations
- Field Logic Controller
- Industrial Cloud
- Industry 4.0
- IO-Link
- Machine Safety
- Modular Machines
- Module Type Package
- Multiprotocol Ethernet
- Pick-to-Light
- Profinet
- RFID
- Snap Signal
- Sustainability
- The Visual Factory