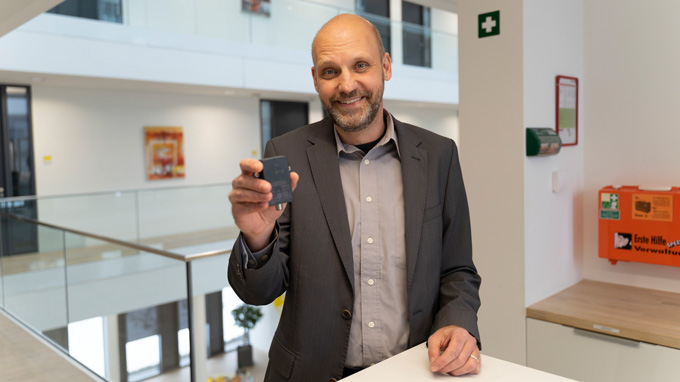
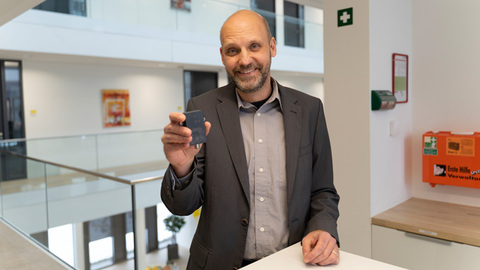
Product Manager Michael Troska is convinced about the benefits of sensor fusion for the user
Inclination Sensors with Fused Measuring Principle
MEMS sensors – the abbreviation stands for “Micro Electro-Mechanical Systems” – measure minute changes such as acceleration. The compact allrounders are now used in numerous devices, including Turck’s new inclinometers, which also house a gyroscope and enable unprecedented dynamics with the fused measurement principles. Turck product manager Michael Troska explains the benefits of sensor fusion for the user in an interview with messweb creator Dirk Schaar.
The topic of sensor fusion and the advantages it offers have been discussed in industry for some time. How long has Turck been involved with this?
We have for a long time offered inclinometers for a wide variety of mobile applications, such as construction vehicles, excavators, cranes, wheel loaders or other vehicles, but also in the conventional industrial sector, for example for dancer control in the paper and textile industry. Many tasks can be successfully solved with conventional inclinometer technology, but for certain applications, sensor technologies that are fused are simply better. We have therefore been working on sensor fusion for some time and have now presented the first devices, with IO-Link interface and the fusion of gyroscope and MEMS accelerometer.
What are the limits of conventional inclinometers?
Conventional inclinometers typically use accelerometers that use the earth’s gravity as a reference signal. If the sensor is tilted, it measures a different acceleration, as it is no longer perpendicular, but this is important for the angle calculation. If we now have disturbance accelerations in the application, for example due to vibration, shock or during acceleration, braking or cornering, the measurement signal is distorted. Most manufacturers use filter functions to smooth the output signal and thus reduce the interference. However, the filters have a decisive disadvantage: They make the output signal very slow and fast movements may not be detected correctly by the sensor because they are filtered out. That’s why we developed the fused sensors.
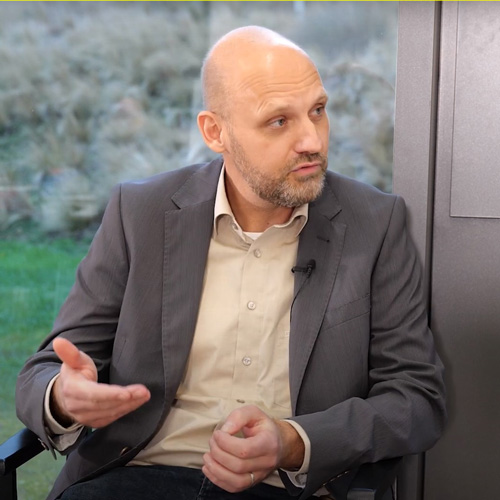
What are the benefits to the user of fusing MEMS and gyroscope signals?
Besides the MEMS accelerometer, we use a gyroscope that records angular velocity in degrees per second. Key benefit: Gyroscope signals do not respond to acceleration. When I combine the accelerometer and gyroscope signals using a smart fusion algorithm, I get an output signal that is extremely responsive and extremely accurate, even in moving applications.
For which applications are these sensors especially designed?
I mainly see application areas on mobile machines. Let’s imagine, for example, an AGV, i.e. a driverless transport system that is constantly on the move. If, for example, this vehicle constantly moves in a curve, then you have a constant disturbance present, a disturbance acceleration. A conventional inclinometer cannot filter out this interfering acceleration because it is constantly present. And that’s why I see the best fields of application particularly in dynamic mobile applications that require a fast response time from the sensor.
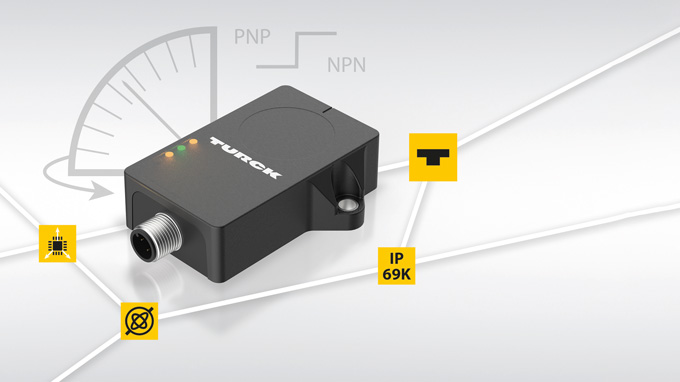
The high dynamics that can be achieved in moving applications are supported by IO-Link. Another benefit, therefore, for the customer in terms of more precise and faster results? If yes, why?
We generally rely heavily on IO-Link because the protocol can transmit additional information besides the actual user data and has other advantages as well. With our inclinometer series, for example, the temperature is recorded in addition to the angle data, as is the number of operating hours. Furthermore, IO-Link also makes it possible to read out information about the application in addition to the sensor information. This is significantly more than an analog interface with 4-20 milliamps can offer. And because communication via IO-Link is very EMC-stable, the user can use unshielded, three-core cables and thus save costs.
A special feature of your sensor is the so-called LED spirit level. What is the purpose of this?
The spirit level is an installation aid. This means that the user does not first have to link the sensor with the controller during installation in order to deliver the process value. The user simply receives direct feedback from the sensor as soon as it is supplied with 24 volts. The yellow LEDs are permanently lit when the sensor is within a window of ±0.5 degrees around the zero position.
There are already further developments of these sensors at Turck. What can we expect?
After first using MEMS cells in our inclinometers to suppress disturbance vibrations, we are now also using them in our new CMVT vibration sensors. Here they do the opposite, and accurately capture and output the vibrations. CMVT stands for condition monitoring, vibration and temperature, because this is also measured by the sensor. When users read out the process data of our sensor via IO-Link, i.e. the vibration velocity, they can easily determine a possible hazard potential in their machine. If the vibration value increases gradually over time or the limits of ISO 10816-3 are exceeded, then the user knows that action is needed before greater damage occurs.
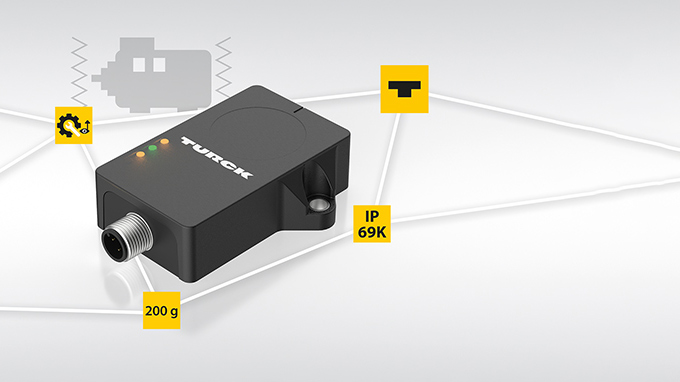
The sensor data also helps to carry out targeted maintenance intervals, i.e. neither too late nor too early, because that also costs money. The CMVT is also provided with switching outputs in addition to IO-Link. The user can therefore easily parameterize the sensor so that the switching output responds when set limit values are exceeded. You can then, for example, control a tower light that lights up green, yellow or red. All this fully autonomously without any controller integration required. Our Turck Vibration Monitor simplifies sensor commissioning and operation. The tool visualizes the vibration and temperature data live in any web browser and can be used easily via any Turck IO-Link master – without any additional software required. This allows the user to view the measured vibration information over a period of time, and if required, the data can be exported to Excel for further analysis.
Author | The interview was conducted by Dirk Schaar, editor-in-chief of messweb.de and GOing
Further Information
- Technologies
- Asset Monitoring Gateway with Cloud ID
- Asset Monitoring Gateway with SNAP ID
- Codesys
- Condition Monitoring
- Ethernet in Hazardous Locations
- Field Logic Controller
- Industrial Cloud
- Industry 4.0
- IO-Link
- Machine Safety
- Modular Machines
- Module Type Package
- Multiprotocol Ethernet
- Pick-to-Light
- Profinet
- RFID
- Snap Signal
- Sustainability
- The Visual Factory